مخطط تفصيلي
- مقدمة
- What Are the Main Market Requirements for MOVs Today?
- How is Longjoin Electronics Innovating MOV Design and R&D To Improve Their التحكم الضوئي Products?
- What Future Trends Will Define the Next Generation of MOV Technology?
- خلاصة القول

الصورة مقدمة من: ariat-tech
Surge protection is no longer just a safety feature—it’s a critical performance demand. As electronic systems grow more sensitive and interconnected, the role of Metal Oxide Varistors has become central.
Industries including the photocell manufacturers now require MOVs that can handle high energy, respond instantly, and endure years of service.
Meeting these demands takes more than standard engineering—it takes innovation. That’s where Longjoin Electronics is changing the game, pushing the boundaries of MOV technology to match tomorrow’s needs.
What Are the Main Market Requirements for MOVs Today?
Modern electrical systems face more frequent and intense surge events. From smart grids to consumer electronics, all demand stronger, faster, and longer-lasting protection. Metal Oxide Varistors (MOVs) sit at the heart of this defense. But not every MOV is equal.
The market now expects performance across four critical areas: energy absorption, voltage range, speed, and durability.
Let’s break down these requirements based on current benchmarks and application demands. Before that, below is a table discussing MOV selection parameters by application type.
مجال التطبيق | Typical MOV Voltage Rating | Clamping Voltage Range | تصنيف الطاقة (جول) | Priority Feature |
Residential Electronics | 130–275 VAC | 215–710 V | 10–200 J | Fast response time |
Industrial Equipment | 320–750 VAC | 600–1500 V | 200–600 J | High energy absorption |
Smart Meters | 150–320 VAC | 250–600 V | 50–150 J | Long lifespan |
EV Charging Stations | 480–1000 VDC | 800–1750 V | 300–500 J | Wide operating voltage range |
High Energy Absorption Capacity
MOVs must absorb a large surge of energy without damage. Standard types handle from 10 J to 600 J; some disk MOVs support up to 600 J, with ring/medium-voltage types rated much higher.
Energy absorption scales with MOV volume: doubling thickness or area doubles capacity. High-capacity MOVs prevent fire risk by distributing heat across zinc-oxide grains instead of concentrating thermal stress.
Wide Operating Voltage Range
Markets require MOVs to perform across varying voltages. Typical units cover AC 130–1000 V and DC 175–1200 V. Here is how this range benefits:
- Ensures compatibility from household supplies to industrial systems.
- Clamping voltage (peak clamp) typically spans 215–1750 V, ensuring protection for systems from low voltage to high power.
- Consistent clamping across conditions is essential to safeguard sensitive circuits without nuisance trips or failures.
Fast Response Time
MOVs act faster than spark gaps—reacting within <20–25 ns, up to 40–60 ns under real-world layouts. This nanosecond-level action is crucial because voltage spikes can peak in microseconds.
Quick clamp prevents energy from reaching sensitive components. MOV response is far faster than GDTs (microseconds), making MOVs vital for early-stage surge suppression.
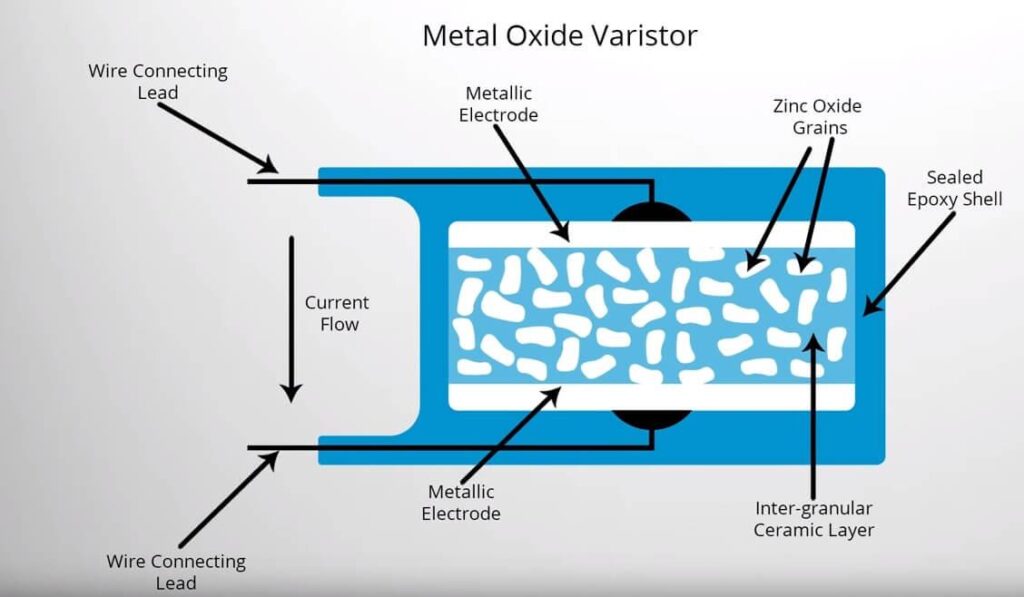
الصورة مقدمة من: ariat-tech
Long Lifespan and High Reliability
MOV lifespan is tied to energy rating and the number of surges. Each clamp slightly lowers the clamping voltage; devices degrade over time. High-energy MOVs can withstand more pulses and last longer. Reliable designs include:
- Thermal fuses or internal disconnects to avoid fire once the MOV degrades.
- Leakage current, i.e, <20 µA at rated voltage,
- High insulation resistance, i.e, ~1000 MΩ,
This ensures minimal standby loss and stable operation.
How is Longjoin Electronics Innovating MOV Design and R&D To Improve Their التحكم الضوئي Products?
To stay ahead in surge protection for their مفاتيح الخلايا الضوئية, Longjoin Electronics blends advanced materials, smart design, and real-time monitoring.
Their approach targets four major areas: مستشعر الضوء quality, internal layout, material innovation, and proactive diagnostics. Each area addresses core surge demands with measurable, modern solutions.
Adoption of Advanced Surge Protection Components
Longjoin sources cutting-edge hybrid components like Bourns’ GMOV™, which combines MOV and gas discharge tube technology. These hybrids deliver enhanced performance, reducing leakage and thermal stress.
By integrating hybrid devices, longjoin cuts component count in half while maintaining fast action under heavy surge loads. This method boosts reliability and cuts board space without compromising protection.
Here is a detailed comparison table of traditional VS hybrid MOVs.
ميزة | Traditional MOV | Hybrid MOV (e.g. MOV + GDT) |
Thermal Stability | معتدل | عالي |
Leakage Current | أعلى | أدنى |
وقت الاستجابة | ~25 ns | 20–30 ns (slightly slower) |
Longevity (surge cycles) | معتدل | Extended |
وضع الفشل | Risk of thermal runaway | Controlled disconnect |
Optimization of MOV Configuration
longjoin tailors MOVs in parallel and series based on dynamic modeling. Parallel pairing of identical MOVs balances current load and extends lifespan, leveraging industry findings that matched devices share stress evenly.
Series configurations raise voltage handling in أجهزة استشعار إضاءة الشوارع while maintaining standard clamping levels. Packaging design places MOVs close to surge entry, reducing PCB trace inductance and preserving nanosecond response speeds.

Innovation in Materials and Processes
Their R&D team explores advanced zinc-oxide compounds and doping techniques. Industry-wide trends toward miniaturized MLCC-type chip MOVs with tailored oxide mixtures support higher energy absorption in compact sizes.
Longjoin’s proprietary sintering process improves grain boundary conductivity, delivering lower clamping thresholds with less leakage.
These material gains meet automotive-grade specs and ensure MOV stability in extreme environments.
Intelligent Monitoring and Early Warning
Longjoin embeds thermal fuses with integrated temperature sensors and status LEDs for visual life alerts. As noted by industry safety standards, thermal disconnects prevent catastrophic failures by isolating worn MOVs.
Their latest modules report real-time leakage current and clamping voltage over the CAN bus to centralized control systems.
This data runs predictive analytics to schedule maintenance before failure. The result: smarter مفاتيح مستشعر الضوء with high uptime and fewer hidden protective failures in high-value systems.
What Future Trends Will Define the Next Generation of MOV Technology?
MOV technology is evolving fast. Demand now calls for greener and more resilient protection. Next-gen MOVs must repair themselves, shrink via advanced materials, fit modular standards, and integrate seamlessly. The table below showcases emerging material in MOV R&D.
Material Type | Benefit for MOVs | Current Limitation |
Graphene | Excellent thermal and electrical transfer | High production cost |
MXene | High conductivity, lightweight | Chemical instability in air |
Polymer Composites | Self-healing potential | Lower energy handling |
Doped Zinc Oxide | Enhanced clamping precision | Limited to lab-scale usage |
Further, here’s a look at emerging directions reshaping surge protection.
Self‑Healing Surge Protection Technology
Researchers are developing MOVs that can autonomously repair micro‑cracks using embedded polymers or capsules. This approach mimics self‑healing materials in coatings and concrete, healing damage without external intervention.
For MOVs, this means restored electrical pathways and extended lifespan. Early prototypes use microencapsulated healing agents within the varistor matrix.
These agents release when stress-induced micro-cracks form, sealing them and maintaining clamping efficacy.
Application of Nanomaterials
Nanotech is enabling compact, high-performing MOVs. 2D materials like graphene and MXene enhance conductivity and thermal dispersion. Meanwhile, research into self-healing nanomaterial electrodes shows dynamic crosslinking for durability.
For MOVs, this translates to smaller chips that absorb energy like larger disks while resisting degradation. Nanocoatings also improve heat management, lowering hotspots during surges.
Standardization and Modular Design
The MOV industry is moving toward standardized, swappable modules. Verified Market Reports highlights demand for high-density, miniaturized MOVs across IoT, EVs, telecom, and renewable systems.
Modular form factors simplify integration into smart grids and EV inverters. Standardized voltage and size tiers mean manufacturers can mix and match MOV blocks to scale protection up or down without redesigning PCBs.
خلاصة القول
Surge protection is entering a smarter, more resilient phase. Longjoin Electronics is clearly ahead with its forward-looking MOV strategies. For reliable access to LongJoin’s advanced photocell and MOV solutions, تشي-سوير remains a trusted sourcing partner.