Outline
- Introduction
- Supplier Management
- Supplier Selection
- Supplier Evaluation
- Supplier Communication
- R&D Stage
- Quality Control (QC) Phase
- Inspection Instructions
- Inspector Training
- Incoming Materials
- Incoming Inspection
- AOD Application
- Stock-in (Materials)
- Production Process
- Finished Product Inspection
- Final Words
In today’s competitive market, production efficiency should be in line with quality concerns to achieve customer satisfaction. This is especially true for photocontrol production, where precision and reliability are paramount.
At Long-Join, robust quality management processes play a crucial role in meeting these demands. From stringent supplier management to comprehensive quality control at every stage of production, Long-Join’s systematic approach enhances both efficiency and the final product’s reliability.
This in-depth analysis will explore how supplier evaluations, material inspections, and process controls contribute to Long-Join’s photocontrol production excellence.

Supplier Management
Supplier Selection
Long-Join selects its suppliers through a thorough vetting process to ensure that they meet specific technical and quality standards. Critical factors include the supplier’s ability to meet industry standards like NEMA and IP ratings. These components need to meet stringent electrical and optical properties to ensure consistent light detection and response.
Furthermore, suppliers must prove their ability to adhere to specific material compositions, such as silicon photodiodes for infrared-sensitive or cadmium sulfide (CdS) for analog photocontrols.
Supplier Evaluation
To ensure that the raw materials meet the required technical standards, Long-Join conducts detailed supplier evaluations. For example, silicon-based photoresistors undergo temperature cycling tests to guarantee they maintain performance across various environmental conditions.
Suppliers are also evaluated for their compliance with international safety and environmental standards such as RoHS and ISO certifications. This ensures that materials contribute to sustainable and safe production processes.
Supplier Communication
Maintaining transparent and continuous communication with suppliers is vital to ensure the reliability of material supplies. Long-Join regularly updates suppliers on changes in material specifications, such as adjustments in photoconductive material coatings or updates to environmental resistance features.
This targeted approach to supplier management allows Long-Join to uphold high standards in photocontrol production, contributing to both efficiency and product quality.
R&D Stage
At Long-Join, the Research and Development (R&D) department plays a pivotal role in defining the inspection requirements. These requirements are developed based on specific parameters such as sensitivity to light, durability in outdoor conditions, and electrical conductivity.
Further, the detailed criteria define acceptable ranges for material thickness, dopant concentration, and uniformity to maintain high light detection accuracy. Additionally, inspection guidelines are outlined for encapsulating materials like glass or epoxy resin, ensuring they provide sufficient protection against moisture, dust, and temperature fluctuations.
R&D also collaborates closely with the QC department to develop mechanical inspection parameters. These include stress tests for durability under mechanical strain and environmental testing protocols to evaluate the photocontrol’s performance under extreme weather conditions.
Quality Control (QC) Phase

Inspection Instructions
The QC department at Long-Join plays a crucial role in ensuring the standardization of photo control. This is done by issuing instructions that cover every stage of the production process and focus on the following areas:
Material Inspection: Guidelines are provided for checking the purity, thickness, and uniformity of the semiconductor materials. This is critical for the light-detection performance of the photocontrol.
Dimensional Accuracy: Inspection criteria include verifying the dimensions of the photocontrol and design tolerances for elements like lenses, encapsulation, and metal contacts.
Electrical Testing: QC specifies tests to measure electrical characteristics, such as resistance, voltage thresholds, and light sensitivity. This confirms that the photocontrol reacts within the required light intensity range.
Environmental Durability: Instruction manuals include protocols for performing accelerated aging tests, such as exposure to moisture, temperature extremes, and UV radiation. This ensures the photocontrol’s long-term reliability in outdoor conditions.
Inspector Training
Inspectors undergo specialized training to recognize material imperfections. This includes micro-cracks in semiconductors or contamination in encapsulation materials. Hands-on training on the use of precision instruments like optical microscopes, multi-meters, and environmental chambers is also provided.
Lastly, training also includes interpreting test data accurately, using statistical tools to analyze results from batch testing, and identifying any potential process deviations that might affect quality.
Incoming Materials
Incoming Inspection
When raw materials arrive at Long-Join, they undergo a rigorous inspection to ensure they meet the quality standards required for photocontrol production.
Key materials like silicon wafers, conductive metals, and glass encapsulations are checked for physical defects, dimensional accuracy, and material purity. For example, the semiconductor’s light sensitivity is tested to ensure it meets performance specifications.
Non-conforming materials that fail to meet these criteria are promptly returned to the supplier. This minimizes the risk of defective components entering the production line.
AOD Application
In some cases, if raw materials show minor defects that don’t compromise overall functionality, the purchasing department may apply for Acceptance of Defect (AOD). This allows the materials to be used under special conditions with approved modifications, reducing waste while maintaining production flow.
Stock-in (Materials)
Once materials pass inspection or receive AOD approval, they are stored in the inventory. These qualified materials are cataloged and preserved in a controlled environment to maintain their integrity and make them ready for the production process.
Production Process
In Long-Join’s production process, each step is responsible for maintaining product quality through self-inspections. Operators are trained to monitor their own work, using inspection guidelines tailored for photocontrol components. This could be checking the alignment of light sensors or ensuring the proper assembly of conductive contacts, etc. This self-control mechanism helps to identify and resolve issues early in the production chain.
Further, routine inspections by the QC department add another layer of scrutiny. QC staff perform frequent checks at key stages of production, ensuring consistency in areas like electrical performance and structural integrity.
Additionally, random sampling inspections are conducted on finished products to evaluate overall quality, including light sensitivity and durability tests, ensuring compliance with both internal and industry standards.
Finished Product Inspection
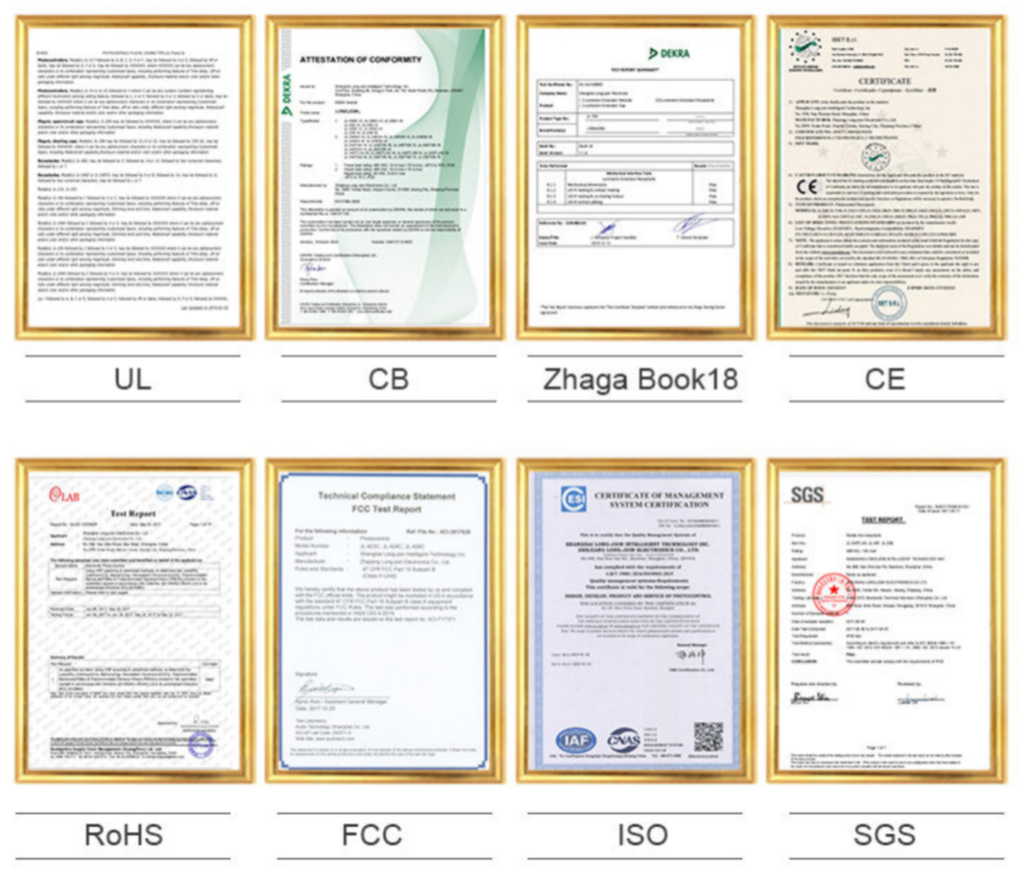
Once photocontrols pass the necessary production inspections, they are transferred to the warehouse and recorded as approved stock. These finished products are stored under controlled conditions to preserve their integrity until shipment.
For added assurance, customers or third-party agencies often conduct their own final inspections to verify the quality of the product. Long-Join adheres to various industry standards such as UL, and ISO 9001 for quality management, CE marking for safety, and RoHS compliance for hazardous material restrictions.
Third-party inspectors may perform tests on light sensitivity, durability, and environmental resistance, ensuring the photocontrols meet both regulatory and customer-specific requirements.
Throughout the inspection process, Long-Join collects quality feedback. This data helps the company refine its processes and resolve any recurring issues, ensuring continual improvement in both product reliability and production efficiency.
Final Words
Long-Join’s rigorous quality management processes, from supplier selection to final product inspections, ensure the consistent production of high-quality photocontrols. These steps enhance both production efficiency and product reliability. For companies seeking a dependable partner for photocontrol manufacturing, Chi-Swear stands out as a trusted supplier, delivering the precision and quality required for Long-Join’s stringent standards.