Outline
- Introduction
- Supplier Material Inspection (IQC Process)
- Material Receipt and Verification
- Detailed Inspection and Testing
- Approval and Documentation
- In-Process Quality Control (IPQC Process)
- Inspection at Each Production Stage
- Handling Non-Conforming Products
- Finished Product Inspection (OQC Process)
- Steps for Final Product Inspection and Approval
- Customer Acceptance and Feedback Mechanisms
- Customer Inspection and Handling Non-Conforming Products
- Process for Customer Verification and Returns
- Corrective and Preventive Measures for Returned Items
- Final Words
Long-jion has carved a distinct name in the light controller industry, standing out for its innovation, durability, and commitment to excellence. As a trusted brand, Long-jion specializes in crafting cutting-edge solutions for outdoor lighting systems, addressing the needs of smart city infrastructure and sustainable energy management.
In the world of light photocells, quality is not a standard; it’s a necessity. Every element needs to work flawlessly in all places-from the severest winters to the hottest summers. That’s why quality at every stage of production is very critical in bringing out products customers can trust for years to come.
This article delves into Long-jion’s meticulous quality control process, detailing how supplier material inspections, in-process monitoring, and finished product evaluations come together to ensure consistently high-quality and reliable photo controllers.

Supplier Material Inspection (IQC Process)
At Long-jion, the IQC process is a critical first step in ensuring the excellence of light sensors. This meticulous procedure involves several key stages:
Material Receipt and Verification
Upon arrival, all raw materials and components are logged into the inventory system. Each item is cross-referenced against purchase orders to confirm accuracy in quantity and specifications. This initial verification ensures that what is received is exactly what was ordered.
Detailed Inspection and Testing
Following receipt, materials are put under intense scrutiny with highly advanced equipment for testing. XRF analyzers are used to inspect material composition according to the standards required.
The dimensional accuracy is evaluated by using CMM, confirming that components meet precise design tolerances. Additionally, Durometers measure the hardness of the material to ensure durability, and microscopes come in handy to inspect the surface for defects at the micro level.
Approval and Documentation
Materials that pass all inspection criteria are approved for production use and moved to the appropriate storage areas under controlled conditions to preserve their integrity. Comprehensive records of inspection results are maintained, providing traceability and facilitating continuous improvement in our quality control processes.
In-Process Quality Control (IPQC Process)
At Long-jion, the In-Process Quality Control (IPQC) process is integral to maintaining the high standards of photocells. This process involves systematic inspections at each production stage to ensure that any deviations are promptly identified and addressed.

Inspection at Each Production Stage
During assembly, operators perform visual inspections to verify components’ correct placement and orientation. Automated Optical Inspection systems are employed to detect soldering defects, component misalignments, or missing parts. Functional testing is conducted to assess sub-assembly’s performance, ensuring they meet specified electrical parameters.
Handling Non-Conforming Products
When a non-conformance is identified, the affected item is immediately segregated to prevent unintended use. This segregation may involve labeling, tagging, or isolating non-conforming items in designated areas or within digital systems.
A root cause is determined with the help of tools like the 5 Whys or Fishbone Diagrams, and after this, the specific issue will be corrected by taking corrective action and preventive measures to avoid it from happening again. All incidents of nonconformity are thoroughly documented, giving a rich source of data for quality improvement in the future.
Finished Product Inspection (OQC Process)
At Long-jion, the Outgoing Quality Control (OQC) process is the final checkpoint to ensure photosensors meet stringent quality standards before reaching customers. This comprehensive procedure encompasses several critical steps:
Steps for Final Product Inspection and Approval
Manual Inspection
Quality inspectors thoroughly inspect each finished product. This meticulous examination focuses on identifying any physical defects, ensuring that the product’s appearance and construction adhere to high-quality standards.
Functional Testing
Beyond visual assessments, functional tests are conducted to verify that each light controller operates as intended. This includes evaluating electrical performance, response times, and overall functionality to confirm compliance with design specifications.
Packaging Inspection
Re-inspection at this step guarantees that only flawless products proceed to the packaging stage, maintaining the integrity of the final product delivered to customers.
Pre-Delivery Inspection
Before dispatch, a final random quality inspection is done. This additional confirms that the batch meets all specified quality criteria before shipment.
Customer Acceptance and Feedback Mechanisms
Long-jion places significant emphasis on customer satisfaction and actively seeks feedback to drive continuous improvement:
Customer Feedback Collection
Longjoin employs a systematic approach to gathering customer feedback, including surveys and direct communication channels. This proactive engagement allows us to understand customer experiences and identify areas for enhancement.
After-Sales Support
In the event of any issues, our after-sales team is committed to providing preliminary solutions within 16 hours of receiving a complaint. We establish detailed after-sales records and furnish customers with the necessary documentation to address their concerns effectively.
Continuous Improvement
LongJoin scrutinizes feedback attentively to inform product development and quality assurance processes. This helps improve our products and services through customer insights so they can align with the emerging needs and expectations of a customer.
Customer Inspection and Handling Non-Conforming Products
Long-jion prioritizes customer satisfaction by implementing a structured process for customer verification and efficiently managing non-conforming products.
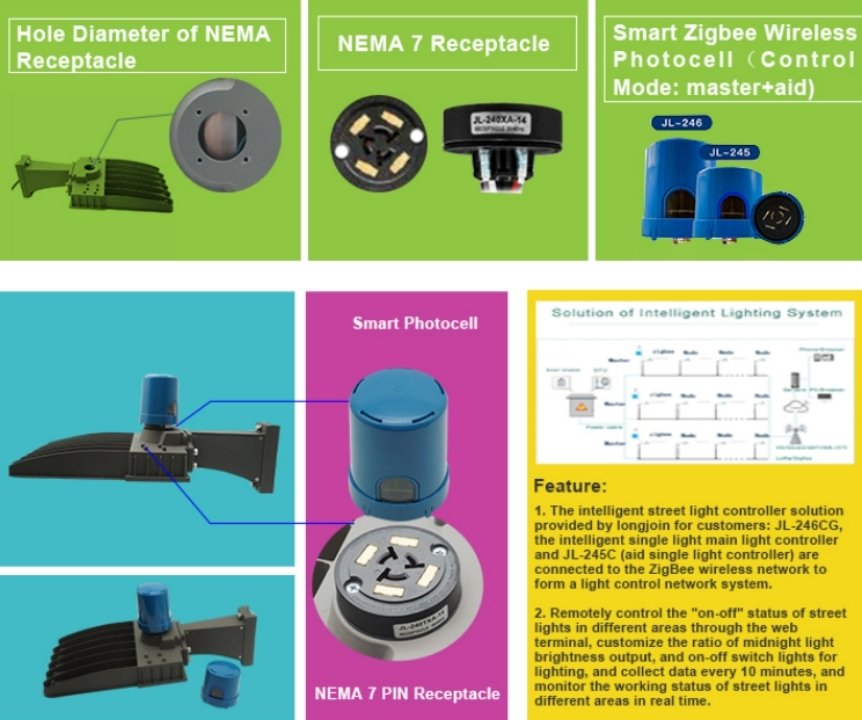
Process for Customer Verification and Returns
- Customers start the return process with a Return Material Authorization request. For this, they require details like the original invoice number and reason for return.
- Upon receipt of the returned product, the company scrutinizes the product to determine what its condition is, thereby verifying the problems raised against it. It is through inspection that the company determines the right course of action.
- The results of the inspection are used to provide suitable compensation to the customers, which can include product replacement, repair, or a credit memo. It helps the customers get speedy and fair settlements.
Corrective and Preventive Measures for Returned Items
- For each non-conforming product, an RCA is done to identify the root causes.
- Corrective actions are targeted to the specific non-conformities based on the findings of the RCA. It may include adjustments in the process, communication with the supplier, or retraining of employees to prevent recurrence.
- Preventive measures in the form of updating standard operating procedures, quality control procedures, or equipment are established to avoid potential future issues.
Final Words
Long-jion’s comprehensive quality control processes—spanning supplier inspections, in-process checks, and final product verification—ensure the delivery of reliable and high-performing light controllers. For those seeking a trusted supplier of Long-jion lighting controls, Chi-Swear stands out as a reliable partner, offering high-quality products backed by meticulous quality assurance and exceptional customer support.